- By Dan Veaner
- Around Town

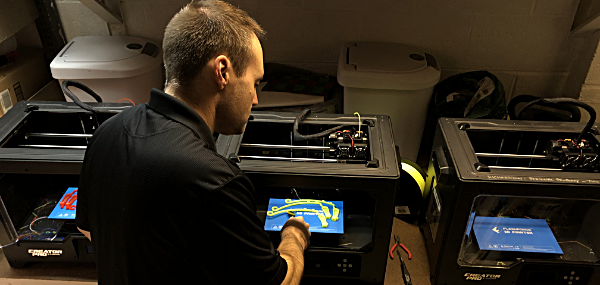
While protective masks help protect medical professionals from infections like COVID-19, face shields add an important layer of protection. A face shield is a piece of transparent plastic attached to a frame something like eyeglasses frames that hook above health care workers' ears and around their head to hold the shield in place. Lansing High School teacher Jeremy Richardson has joined a group of about 100 Tompkins County volunteers who are using 3-D printers to create face shield frames to help battle a growing shortage as the pandemic strains medical resources.
"We have a contact with Weill Cornell Medicine in New York City," Richardson says. "We work with city hospitals that have approved a particular design. Then we make sure that we get some of the changes like the two piece clip-together design approved. The original design that was approved comes in a downloadble STL (Standard Tessellation Language) file. That file was made available to everyone in the group. We've been using the identical file on all the different printers, so all the finished products are exactly the same size and specifications."
Richardson is printing face shield frame halves that clip together to make a single frame. The clear plastic part, manufactured in New York City using laser cutters, is clipped onto the frames to make a shield.
3-D printers consist of a print bed, with a print head that moves above the bed to distribute plastic that is delivered in spools of plastic strands, and melted and placed on the printer bed in layers. The printer knows where to layer the plastic by reading the design from an STL file. They were introduced in 1983. Since that time 3-D printers have become more affordable and versatile, with many models manufactured for personal use.
Today the printers are used by hobbyists to make game pieces, models, and useful objects. The most infamous use of 3-D printing is to make plastic firearms that don't register at airport security. But far more items are 3-D printed for all manner of uses in business and around the home. In fact you can 3-D print a real house, which proponents say can be much less expensive than traditional building methods.
In 2013 NASA awarded a Small Business Innovation Research grant to a Texas firm to study the feasibility of 3-D printing food in space. In 2016 the first 3-D food printer was manufactured, and by 2017 a 3-D pizza printer was installed on the International Space Station.
Richardson bought his own 3-D printer in 2014 when he began teaching at Lansing High School. His first print was a 20-sided gaming die from a design he downloaded from Thingiverse, a Web site where 3-D printer designs are shared. Since then he has created his own designs for clips and fasteners and things that solve everyday problems.
"I knew that at some point we would probably invest in more printers for my classroom. So I bought my own basically to learn as much as I could about the process. So I've had my own for a few years now and it's actually one of the three I'm printing with right now."
The other two printers were purchased for the schools by the Corporate Development Committee (CDC), which raises money to purchase technology for Lansing Schools.
"My freshman 'Project Lead the Way' class especially does so much 3-D modeling in their curriculum," he adds. "That's why I wanted to have the ability to output those 3-D models into physical artifacts that they could see. And in some cases they get to take those designs that they've made and keep them."
Richardson learned of the project through the Ithaca Generator Makerspace, where members gather in person and online to share 3-D printing information and resources. The current president, Elliot Wells, has been publicizing the project and organizing access to supplies. The makers meet in an online Slack group.
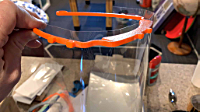
"They want assurance that it's not happening in any unsanitary conditions and that I'm using really careful procedures in terms of not introducing any potential contamination," Richardson says. "So they're being sealed in new Ziploc bags handled in a sanitary way and dropped off in a box for shipment."
The number of frames each maker can produce varies with the size and capabilities of the individual 3-D printers. Using all three printers Richardson estimated he could turn out three shields per hour.
"The nice thing about these prints is that they are a flat piece. Because 3-D printing happens in layers, it's not that many layers of plastic to print before you're done," he says.
While the physical schools are closed, Richardson is providing his students with updates on the project in the hopes that it will inspire them to come up with their own health-care related designs when they can come back to school.
"I posted an update on the beginning of the process and we're just getting started with some online versions of our drawing software," he says. "I'm hoping to not necessarily get into shield production or visor production because that's already an established file, but what I'm hoping to do is, once we're up and running with the new drawing software, to start thinking creatively and getting into some designs that are related to this industry. So other types of protective equipment, other types of health care related accessories. I'm sharing this process as sort of an inspiration for some assignments we'll do later that I think will be relevant."
v16i14