- By Dan Veaner
- Around Town

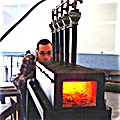
"I am taking a modern approach at a 10,000 year old tradition of making knives in a very bespoke hand made way, and putting a lot more time into it than most modern people do now," he says. "I love working with the metal. I love creating these patterns that you don't get to see until the very end. The whole process is building this thing from a couple of layers to thousands of thousands of layers that are intricately working with each other. And colors and the different types of steel -- it's beyond fascinating for me."
Greenly works mainly with Damascus steel, repeatedly folding the metal upon itself to create thousands of layers that form intricate patterns in the blade. He starts with a steel bar, or a bar made of welded layers of different steels. The bars are heated until they can be drawn out, much like pulling taffy. He stretches the metal, then folds it in half, welding the edges each time to prevent air from getting in where it could degrade the material. With repeated folds the layers grow exponentially. This routine is repeated countless times, folding the metal and bonding it back to the outer surface, always anticipating patterns the folds will create.
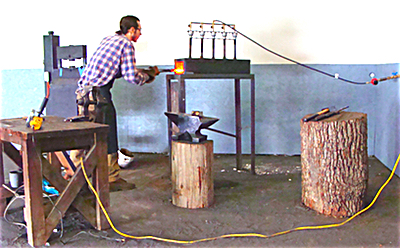
The process is a bit like playing chess. You need to be able to anticipate several moves ahead and you need patience. A lot of patience. Greenly spent almost two months making an 18 inch sword blade that has over 100,000 layers.
While the techniques are ancient, some of the tools are quite modern. His forge, for example, is propane-fueled with valves that control the amount and location of the flame more precisely than an old fashioned wood-charcoal burning forge. It is also cleaner burning, reducing the chance of the steel becoming contaminated. A hydraulic press saves much time and manpower in shaping the metal. But you will also find very traditional tools like a large anvil, hammer, tongs, punches and chisels. He does the shaping and detailing by hand. Greenly says the modern tools replace human apprentices. The finish work is done by hand, including filing, hammering, and polishing that is done in much the same way it has been for centuries.
"I really enjoy the amount of modern materials and time saving equipment that are available now," Greenly says. "Like my hydraulic forking press which lets me draw out materials instead of having two apprentices with sledge hammers working for a month, it take me a couple of days to fold something. It saves me a lot of time to do something that already takes me a lot of time."
Greenly grew up in Lansing, and became interested in blacksmithing at a young age. A visit to the British Royal Museum with his father gave him his first close-up look at intricately crafted Japanese swords. He was immediately hooked.

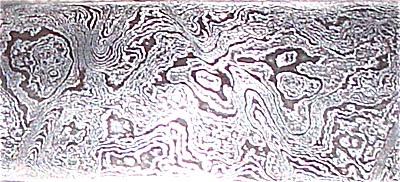
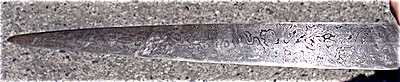
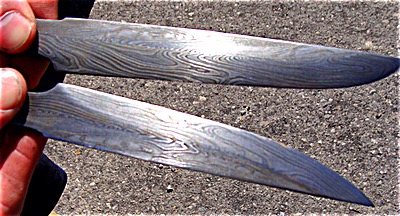
"That's the first time I got a close look at something that took months to build," he says. "The shapes and contrast really spoke to me. It is a beautiful, elegant thing that is also a functional tool. There's somethng about the historical importance of these things. Thousands of years ago the most expensive thing that any person could own was a sword because of the cost of metal and the cost of the skills that it took to own that thing."
He began apprenticing to Mecklenburg blacksmith and artist Durand VanDoren when he was 12. He spent five years under VanDoren learning the basics and working on projects. After a year at art school Greenly decided to build his own portfolio, drawing on books, videos, and an online community of blacksmiths. He reached out to a lot of craftspeople who were generous in answering his questions and proffering advice. Last year he secured a workspace, and began building his portfolio.
"I came back and decided I needed to just do it," he says. "I needed to spend the time. I've been proving myself in leaps and bounds, looking back on my projects."
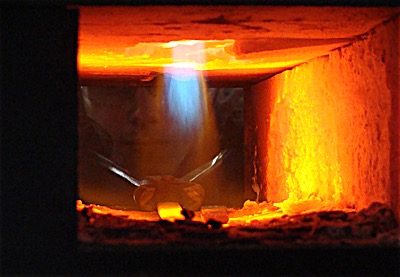
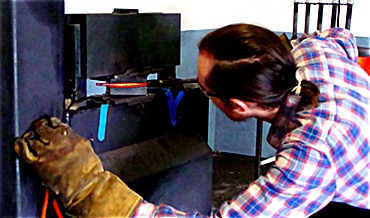
Part of his portfolio will be a large sword project that he estimates will take about a year to complete, including three or four months to finish the blade alone. That will illustrate that he is capable of crafting a larger, more difficult piece. He plans to have a number of finished knives made of high quality materials that he has been collecting for years that will incorporate silver, inlay, and carved wood. In addition to making blades, a finished knife or sword requires a handle, sheath, and sometimes more decorative work including engraving.
"I would love to learn every one of these disciplines, but I could see each one of them taking a whole lifetime," he says. "These skills have been passed down by hand for generations until the Internet. Thousands of years of accumulated lifetimes-worth of knowledge to figure out these things. I feel very lucky that I live in an era when all that knowledge from all these different countries are accessible."
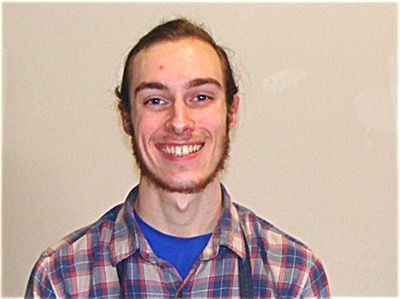
Greenley plans to spend another year building his portfolio, and then hopes to go to gunsmithing school. He says there is a high end market in gun barrels, and he would like to apprentice at one of the major gunsmithing companies.
But if an opportunity arises, he will be wall placed to make a living making blades. A small knife sells for between $500 and a couple of thousand dollars, with the highest-end pieces going for around $5,000. It depends on the quality of workmanship and materials and the reputation of the smith.
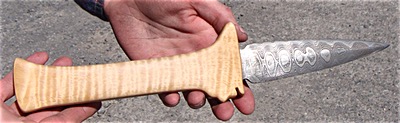
For now he is content to work at his forge, creating intricate, beautiful blades. Working on multiple projects at a time breaks up the repetition, keeping his days varied and interesting.
"There are different stages where I will be cleaning one piece and forging another one," he says. "Not doing the same thing every day lets me move around and do a lot of different things. It's the first time I can decide what I am doing for myself. I don't have to worry about catering to someone else's project. It's super-freeing."
v12i19